Author: electrex
Interview to Luísa Coutinho
“Technological areas, where the demand for qualified technicians is superior to supply, also offer women prospects of interesting and well-paid professional careers.”
On Women’s Day, we interview Luísa Coutinho. Through her professional career we realize that it is possible for a woman to achieve success in the world of welding, if not let’s see: Luísa Coutinho is Executive Director of the European Federation for Welding, Joining and Cutting (EWF), consultant of ISQ (the Portuguese welding institute) in addition to being a PhD in Welding and a professor and researcher in the Mechanical Engineering Department of IST (Instituto Superior Técnico).
Electrex: With so many fields of study in mechanical engineering, what motivated you to follow the field of welding and to do a PhD in this area?
Luísa Coutinho: A good teacher! At Instituto Superior Técnico I had Engineer Dias Alves, from Sorefame, as professor of mechanical technology. He was a great teacher who linked theory to practice and aroused interest in welding technology. Later, ISQ put me in touch with Prof. Apps at Cranfield University, where I went on to do my PhD with a scholarship from the Gulbenkian Foundation.
Electrex: A question we cannot escape: Was it difficult for you as a woman to enter a mostly male world?
Luísa Coutinho: It is well known that in Portugal women find it more difficult to have their skills recognized and promoted in their professional careers than men. My case was no different. With work, dedication and persistence the recognition finally arrived, first internationally and only later in Portugal.
Electrex: In April of last year, you said that Europe is at risk of implosion. Do you still have this concern? What paths should Europe follow?
Luísa Coutinho: Europe continues to experience difficult times, with a mosaic of electoral results in several countries that create situations of political, social and economic instability. Economic growth has, however, brought many positive aspects. I continue to believe in a united and strong Europe.
Electrex: What advice would you give to young women who want to pursue the field of welding either as an area of academic study or as a welder per se?
Luísa Coutinho: Welding and, more generally, manufacturing technologies are not appealing areas for women. I am now in Brazil and today I visited Senai Technological Center, a reference in professional qualification in Brazil. One of the aspects mentioned in the meeting with the Management was the need to make inform of the professional options of welding to secondary school students. We have addressed several initiatives in this direction implemented by European welding institutes.
Technological areas, where the demand for skilled technicians is superior to supply, also offer women prospects of interesting and well-paid professional careers.
Wave forms AC welding
The old TIG machines with conventional technology used the sinusoidal waveform in TIG welding in alternating current (AC). Nowadays, the new inverter TIG AC/DC machines allow the selection of various waveforms in TIG welding in alternating current (AC). This selection, without changing other parameters of welding, allows to change the characteristics of the arc, the seam, and the cleaning / penetration effect.
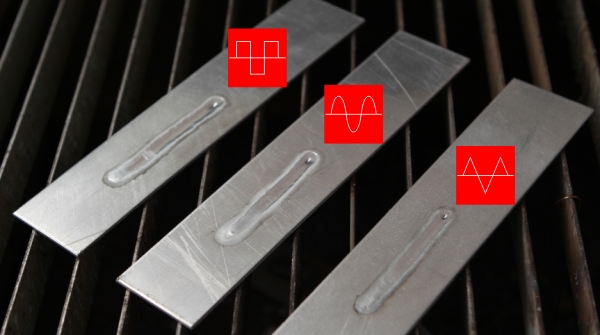
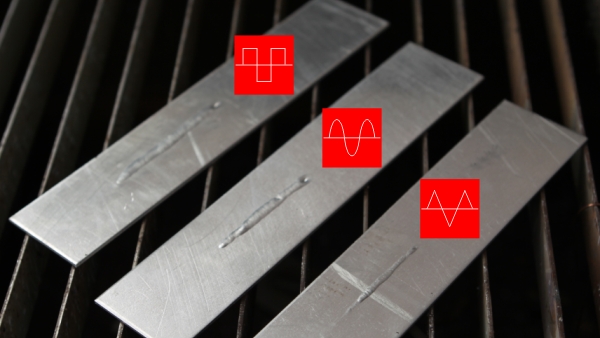
Square wave:

Welding of light alloys with more penetration into thick plates. It forms a more “strong” arc, then more rough and noisy, where there is more heat transfer. It forms a broader and thicker seam.
Sine wave:

Is used in most applications.
The arc is smoother and less noisy than the square wave.
Triangular wave:

Welding of thin plates with little transference energy and thus, less penetration. It reduces the distortion of the parts and allows a fast solidification of the welding bath. It is especially recommended for thin-thickness aluminum.
Weding Visual Inspection
There are many ways to inspect a weld, but one of the simplest, practical to do, is the visual inspection. This is surely a non-destructive testing, which lets you monitor what is happening on the surface with the naked eye or through a magnifying glass. There are other techniques such as radiographic testing or ultrasound testing, which should be part of the quality proceedings. The weld bead, its shape and form, is a major defect indicator in a weld, but not the only: the heat-affected zone, the presence of projections, cracks or distortions in the workpiece, among others are also indicators of welding quality. The most common defects in a weld joint may be due to the following causes:

Falta de penetração
– corrente ou velocidade de soldadura muito baixas
– abertura excessiva da junta
– chanfro inadequado
– grande espessura da peça de trabalho
– distância excessiva entre o eléctrodo e a peça de trabalho
– posição ou movimento do eléctrodo inadequados
– diâmetro do eléctrodo inadequado

Mordedura:
– corrente ou velocidade de soldadura demasiado elevadas

Preparação incorrecta da junta:
– chanfro inadequado
– desalinhamento das peças a soldar

Fissuras:
– Crateras no final da soldadura
– tipo de eléctrodo inadequado
– eléctrodo húmido
– grande espessura da peça de trabalho
– chanfro incorrecto

Excesso de respingos:
– corrente de soldadura muito elevada
– grande distância entre eléctrodo e a peça de trabalho
– peça suja- eléctrodo húmido

Inclusão de escória:
– escória não removida durante passes ou na troca de eléctrodo
– posição ou ângulo de eléctrodos inadequados
– diâmetro do eléctrodo muito elevado ou chanfro muito estreito

Porosidade:
– Peça suja, enferrujada ou húmida
– corrente de soldadura incorrecta
– velocidade de soldadura elevada
– distância excessiva entre o eléctrodo e a peça de trabalho
– eléctrodo húmido

Distorção de contracção e angular:
– corrente ou velocidade de soldadura demasiado elevadas
MIG conventional vs MIG MecaPulse
MecaPulse system for low heat continuous welding with less workpiece distortion and excellent gap bridging of thin plates. Great reduce of wire and energy consumption. Present in MIG/MAG DIGIT II, SYNERGIC II and LTRONIC SYNERGIC machines.